Tuesday, June 27, 2006
Floors and Flaps
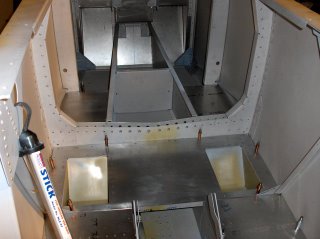

Some issues have come up though:
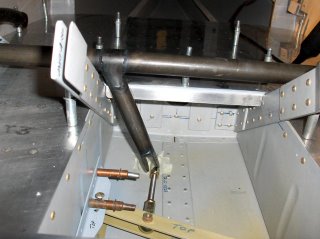

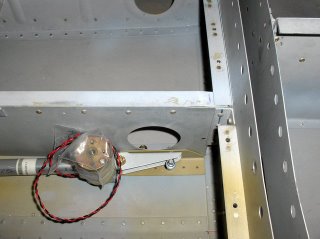

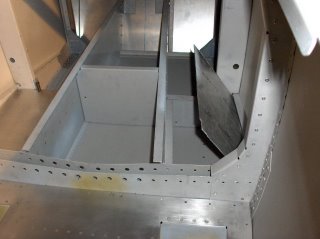

Friday, June 23, 2006
Footwells complete
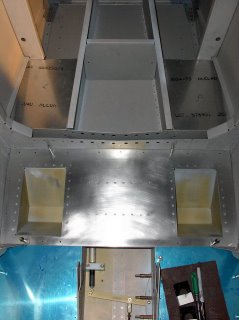


You can find a plan for these in the '24years of the RVator'. If you double click the picture I think you can probably read the dimensions off the enlarged version.
Thursday, June 22, 2006
Footwells
Although not supplied by VANS, even as an option, most RV-4 have footwells for the passenger's comfort. It is worth noting they are pretty well mutually exclusive with rear rudder pedals. (But then you don't build a -4 with the emphasis on someone else having all the fun!) Plans for these footwells can be found in 'RVator 24 years'.
The footwell is riveted together from 3 bits of ally with simple bends. It then has to be set into the floor and a hole cut to size.
Here it is now dropped into the floor. Its still looking a bit
ragged at the edges but nothing a file and patience wont sort out. The black tape is to protect it from the file.
This is the crucial bit. The footwells sit right behind the aileron pushrod path. Once the footwell is set in the floor you need to check the path for the pushrod is clear. Yes, it overlaps a little, but I think this is normal.
One irritation shows up in this picture. You can just see a nut. This is a part of the flap system. It is where it is meant to be according to VANS plans but if I tighten it up it will crush the stamped metal around the push rod hole. It probably doesn't matter, but its a bit ugly.




ragged at the edges but nothing a file and patience wont sort out. The black tape is to protect it from the file.


One irritation shows up in this picture. You can just see a nut. This is a part of the flap system. It is where it is meant to be according to VANS plans but if I tighten it up it will crush the stamped metal around the push rod hole. It probably doesn't matter, but its a bit ugly.
Tuesday, June 20, 2006
Flap drive system
Today I moved on to the flap drive system. I like mechanisms so this is where the fun really starts. The RV4 was originally designed with a manual flap system, however it has some draw backs, in particular its effect on passenger comfort. The electric flap system is therefore an option which was designed in afterwards. As you can see it uses the same flap drive mechanism as the other RV, but has an interesting lever system in view of the limited space.
In this picture you see the drive mechanism on the RHS partially extended; perhaps 10 to 20% of its range. The fixing on the LHS is a pivot point. About 1/3rd of the way along the lever you see a bearing which when the flap motor causes the mechanism to contract moves at about 1/3rd of the rate with 3 times the force. This pulls on a lug attached to the flap actuator (black) and in turn will cause the flaps to be deployed when it is all connected up. The points to watch when you are installing this are that you don't let the motor get too high. The problem this causes is the drive mechanism when fully extended is very close to the floor. I have a shim under the white nylon guide block you can see on the RHS. This will I think ensure the bolt head never touches the floor.
Here the camera is nearly on the floor, looking aft. You can see the same bearing on the lever arm and the lug hanging down to which it will connect.
You can also see something interesting which is nothing to do with the flap mechanism. Projecting forward towards the camera is my solution to the rear passenger 5th point seat belt attachment point. Its not ideal in that the pull will be vertically upward, but I think it is quite beefy enough to do the job. It will need a thin shim between it and the underside of the cockpit floor.
There are quite a few 2 man jobs involved assembling this since some of the brackets need riveting on from underneath the fuselage.
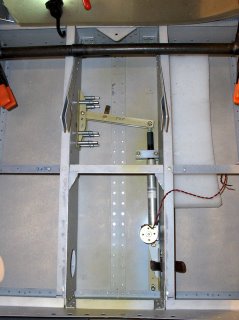

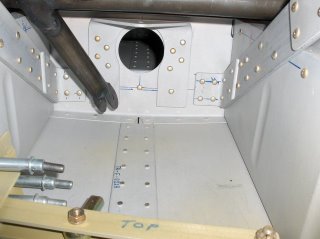

You can also see something interesting which is nothing to do with the flap mechanism. Projecting forward towards the camera is my solution to the rear passenger 5th point seat belt attachment point. Its not ideal in that the pull will be vertically upward, but I think it is quite beefy enough to do the job. It will need a thin shim between it and the underside of the cockpit floor.
There are quite a few 2 man jobs involved assembling this since some of the brackets need riveting on from underneath the fuselage.
Friday, June 16, 2006
Roll bar structure continued.
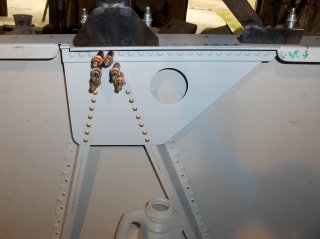

I spent quite a bit of today working on the role bar support structure. The role bar is now clecoed in its final resting place. All the necessary edge distances are good.
The canopy rail is installed and the F-417 is riveted to the bulkheads. I will need to replace the remaining clecos with blind rivets. A few are allowed, though VANS encourages you to buck as many in the space between the skin and the F-417. I cant make that work.


Monday, June 12, 2006
Progress with the roll bar structure.
Support came flooding in from the -4 community regarding the roll bar support structure. Several pictures all of which agreed with each other, and not quite with the plans. That has enabled me to move forward with confidence. (Thanks everyone!)
This is current status.
The angle is riveted to the F-417, and it sits nicely underneath the canopy rail. The forward inch or so even tucks in behind the rail which I think will make it look neater. I no longer need the shim I had made. The need for that went away when I 'unbent' the rail and was able to slide the angle up to its final location. It seems to be going together quite nicely now. The roll bar is sat there for the photo. I haven't touched it with the drill yet.
I still have to cut off the excess material from the flattened out side rail.
In this picture you can see the angle did fit nicely behind the rail at the front end, though not by anything like the amount the plans indicated.
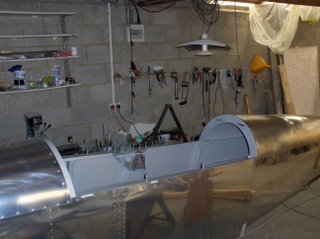
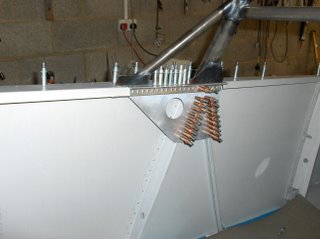
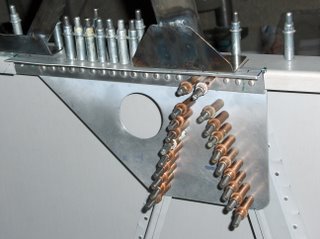
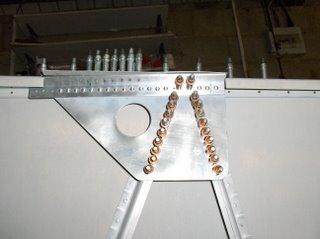
Saturday, June 10, 2006
Rollbar Support Structure: F-416 & F-417
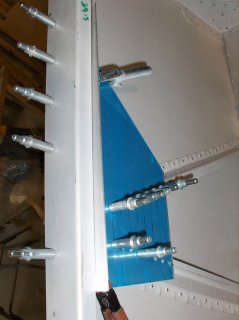

In the first picture I have assembled the F-417 and replaced the canopy rail F-416. I have then offered up the 12"*1"*1" angle. The problem is that according to the plans about 1/3 of the angle should be behind the canopy rail. Even at the front nearly a quarter inch is sticking out.
Read more ยป